How Intelligent Systems Will Be Created In Future?
- Abhijeet Srivastav
- May 19, 2020
- 2 min read
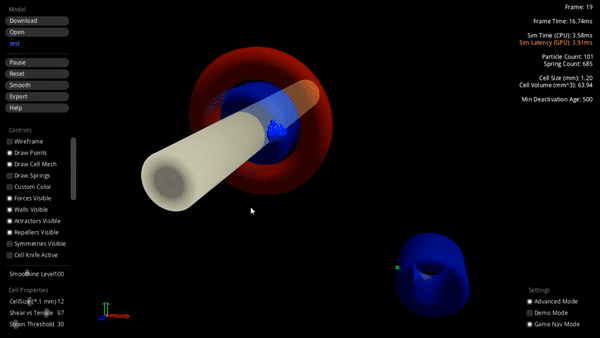
As of now, designing parts for an intelligent system involves building up the parts from the ground up. From 2D sketches to a feasible and robust part that can be manufactured based on given constraints of cost, material, and maximum weight. This often takes days to weeks, depending on the complexity of the parts that comprise the intelligent system.
One must be able to assess the right geometry, shape, design, material of a component so that it can survive the forces that will act upon it.
How it’s done now: Assessing the thickness and geometry required
Engineers spend hours figuring out the ideal geometry required based on given loading conditions.
One can build a straight beam or a truss or a complicated set of beams with ribs between any 2 points.
As of now, most engineers conduct FEA (Finite Element Analysis) on CAD software that takes hours to process and you have to constantly edit the design until you have the correct thickness and geometry based on loading conditions

How it’s done now: Assessing the design for manufacturing purposes
FEA doesn’t tell you what design is good for manufacturing. It is more of an afterthought for even the most experienced designers. Hence printing a part could be expensive given most of it might require a lot of supports.
Excessive support material can drive the costs up.
A good rule of thumb is to follow the YHT rule to prevent excessive supports from being printed. As I stated before, most design software's don’t incorporate this and hence this is left as an afterthought.
How it’s done now: Assessing the material required for intelligent system
For example, if you’re trying to design an intelligent robot with a robot arm to be able to fit in narrow tight spaces and that can survive tensile forces and other heavy loads you need to think of the right material for such a task. You need to have a decent knowledge of material science and mechanical design to choose the right geometry and design.
The tensile stress on the part based on the thickness and loading conditions should not exceed the tensile stress of the material.

AI-Based Generative Design
A new experimental technology called Live Parts is experimenting with the auto-creation of a part based on any given material on its loading constraints. The generated design is ready to be manufactured as it minimizes the amount of support material required and accounts for all the given constraints.
AutoDesk is also experimenting with generative design and is looking to make it a mainstream practice in the design of intelligent systems.

This development can help save hours to weeks of work that goes into creating different parts and considering different constraints such as strength, stiffness, mass, cost, manufacturing time, etc.!
Conversion of 2D sketches and images to 3D models
Further, the conversion of 2D images into 3D models will allow even the most amateur designers to start building faces for intelligent service robots for the purpose of customer service or entertainment.
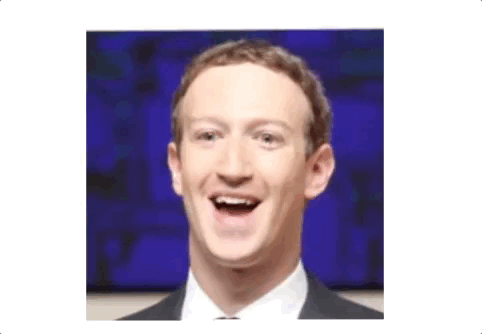
These 3D models of faces can be exported as .obj and then imported into the CAD software to integrate with the rest of the robot.
Comments